My big project lately has been an box organizer for The Guild of Merchant Explorers. It comes with no organization and you just have to stash everything in bags. This makes set up and take down a pain and unnecessarily long.
A couple organizers for the game already exist on the 3D printing websites, but I wanted something better. Something that could stand up to the box being turned sideways or upside down without making a mess. So, naturally, I designed my own to meet my stringent criteria. Also, designing it myself let me spruce it up with premium details.
A challenge of keeping pieces from scattering is that there is space between all the components and the lid when the box is closed. It’s only about 2mm, but that’s enough for cards and bits of cardboard to slide around.
So to accomplish my goal of keeping pieces from going everywhere when the box is turned I created my trays to nest on each other so there’s not enough room for pieces to slide out when they come apart a little bit. This works great, but you’ll have a tray on top with nothing above it. So for that case I printed covers which set into the trays to keep things in place.
The game has 3 decks of cards that you use regularly (and 1 which is used only at set up). As a little nicety I chamfered the bottom of the tray so when you press on the side of the card the other side pops up a little making it easier to grab.
Finally, I added the symbols used in each section of the trays to identify what components go where. Overall, I’m extremely pleased with the final results. Set up and take down are now almost instantaneous. And I already got a request from someone at the board game meetup to print one for them.
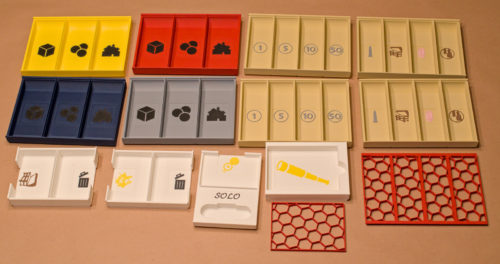
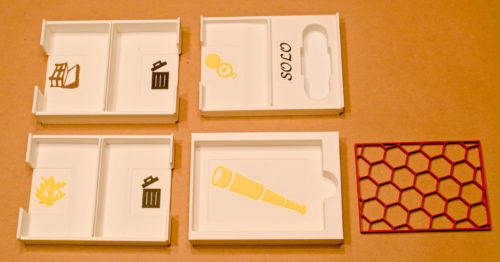
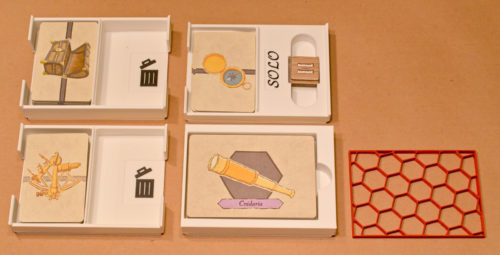
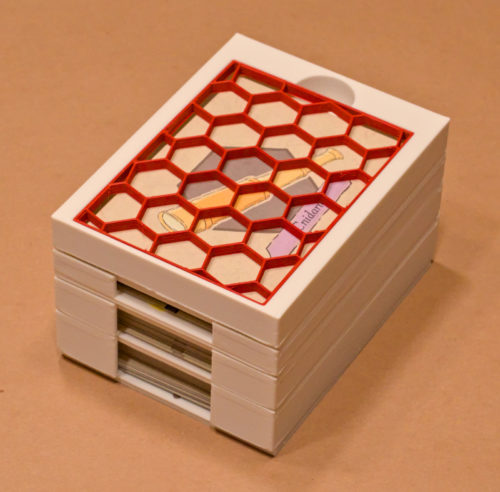
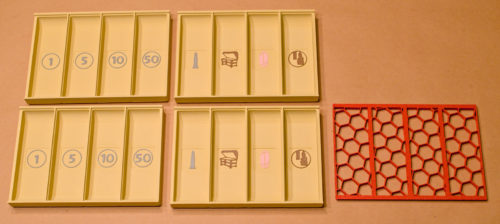
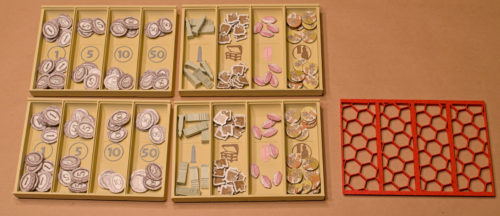
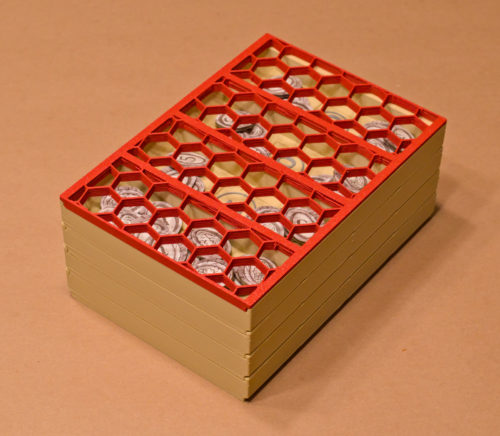
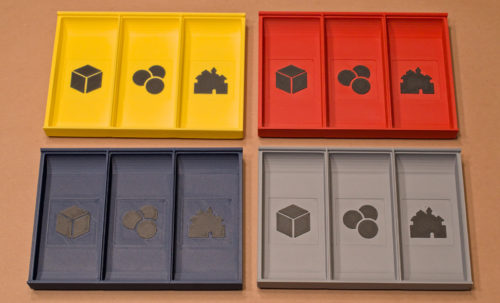
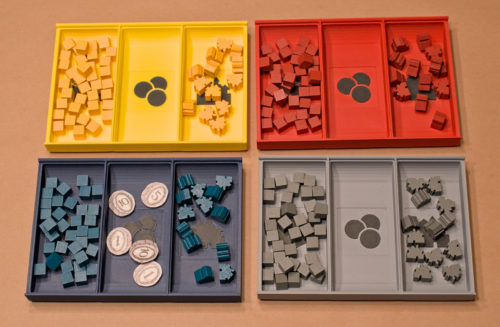
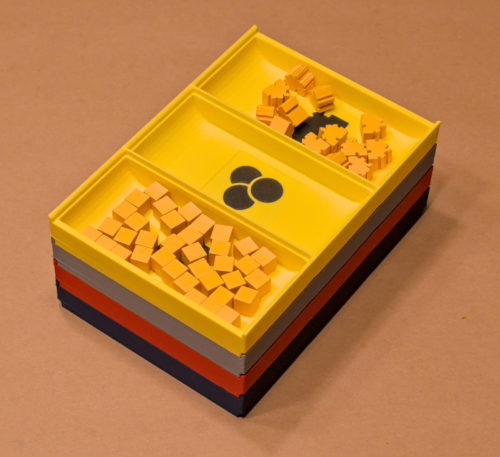
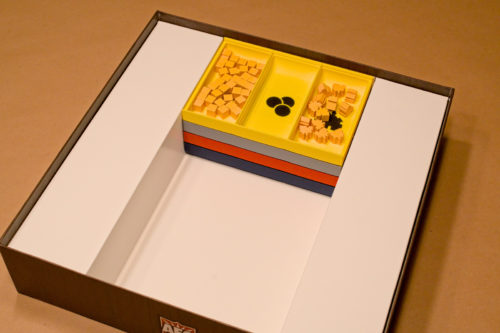
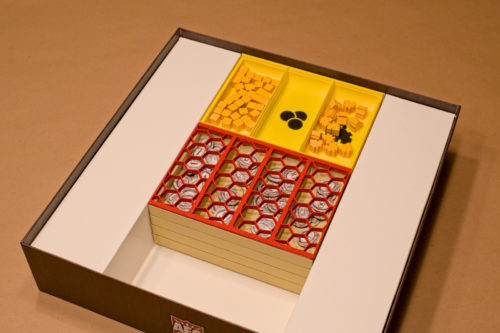
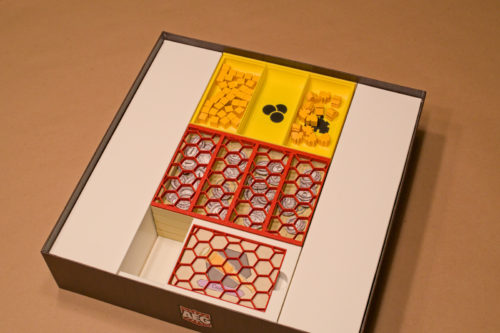
Some of my design notes from the project. I worked on it for about a month before I decided I was happy with it and printed it.
For the last 8 years I’ve organized and run an event at work called Developer Day to encourage software developers to interact with each other and learn about the various projects happening around the Lab.
To encourage attendance and participation I give out door prizes–usually whatever I find interesting off of Amazon. This year I augmented the prizes with some 3D printed things I designed.
First up is building 453. This is the main supercomputer building on site and the building where we’ve been holding the event. I modeled it based on aerial imagery from Google Maps and some educated guesses from first-hand information. Then I put it on a base and added the Lab logo and some text. It’s about the size of a credit card. The big bland block on the back is the machine building where the supercomputers are housed.
Then I played around with a couple of designs of these text blocks. They’re hollow, about 2.5 inches long, and 3/4 of an inch tall.
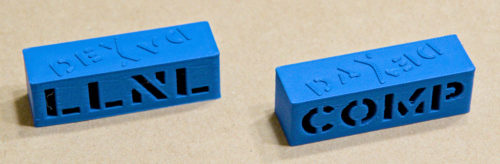
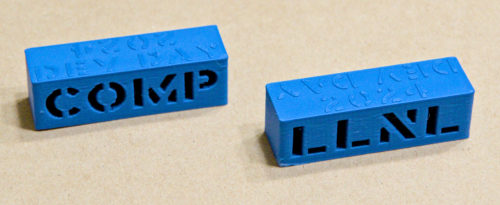
And then I thought it might be fun to do something with light and the translucency of the filament material. So I designed these blocks which show LLNL when light shines through them.
And my final project of the month was modeling the Trinidad Head Light Station in Trindad, CA. One of the projects my team runs is named after this lighthouse and I’m considering printing a few of these for those team members.
I printed this in parts and assembled it after so I could get the differing colors without wasting a huge amount of filament switching back and forth during the print. I’m pretty happy with it. I’m very pleased with how the assembly went.
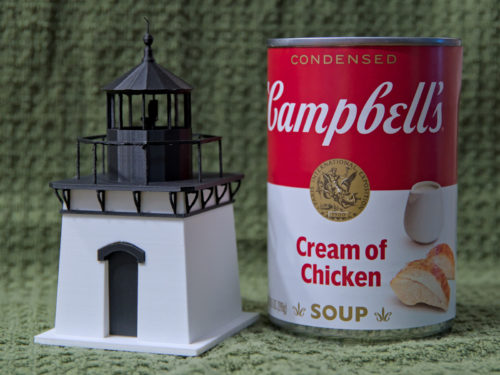
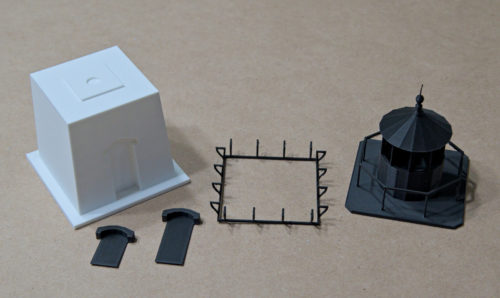
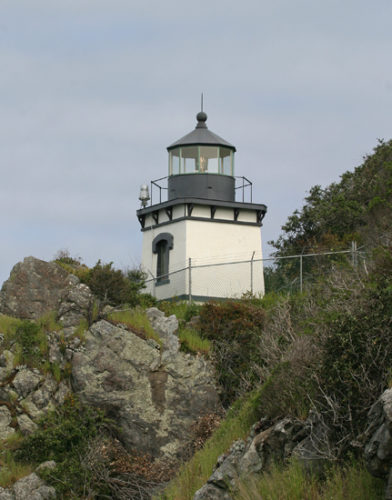
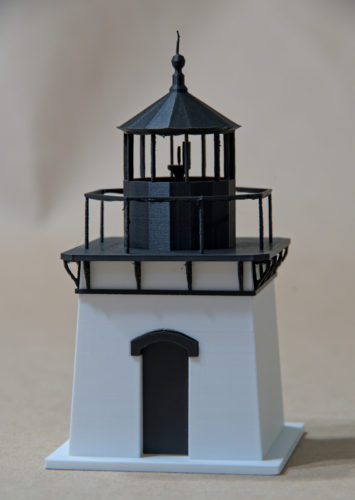
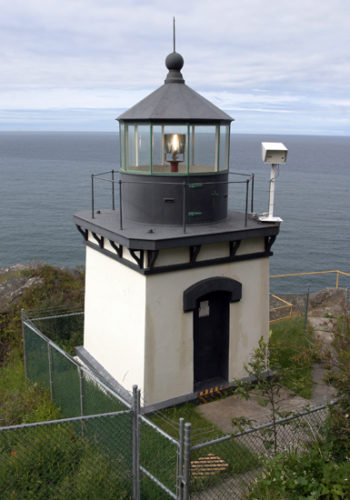